Building biomethane plants: our raison d’etre since 2005
Our technologies
We specialise in the design, build and commissioning of biomethane plants. We adapt our solutions to the different feedstocks you use in order to optimise the operation of your future plant. We design several different processes, including continuous stirred or wet digesters and dry digesters, as well as offering different biogas recovery methods such as biomethane injection and cogeneration.
There are currently three different models:
Monitoring every step of the build
We are present at every stage of your project to guarantee the schedule is optimised and adhered to.
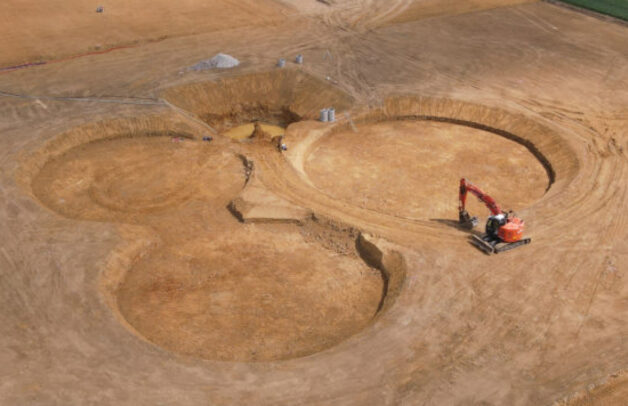
Constructing the foundations
At the start of your project, we strip and excavate the land, create the different platforms that will support the digestion and storage structures and prepare the construction of the concrete tanks.
Building the tanks
Once the platforms are accepted, we construct circular concrete tanks. Our construction method allows us to install the protective lining and thermal insulation at the same time as pouring the tanks. This reduces the overall construction time. Once building is complete and the concrete has set, we carry out water testing to ensure the works are completely watertight.
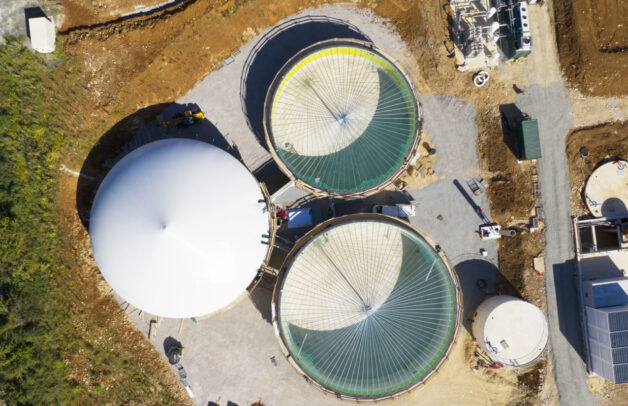
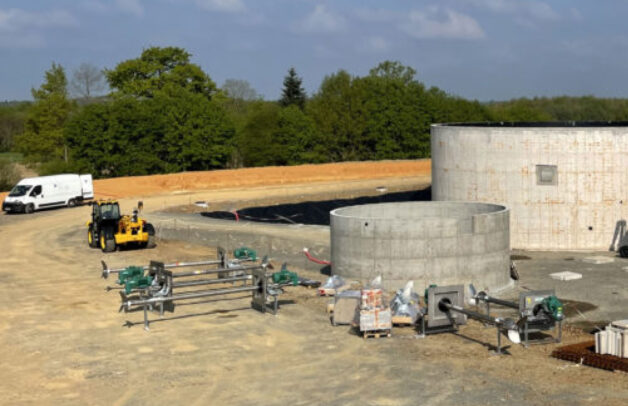
Installation phase
This phase takes place once construction work is complete and involves installing all the mixing, pumping, grinding, agitation and digestate treatment equipment. At this point, we also construct any underground or overground pipelines and install the fuse boxes and cabling for all the equipment.
Automation
The brain of any biomethane plant, the control system is programmed by our control teams to allow you to manage your plant and guarantee its performance. The control system is scaleable and can be modified in line with any changes to the plant. Our supervision software provides operational monitoring of your plant – either on site or remotely – from feedstock loading through to biogas and digestate production.
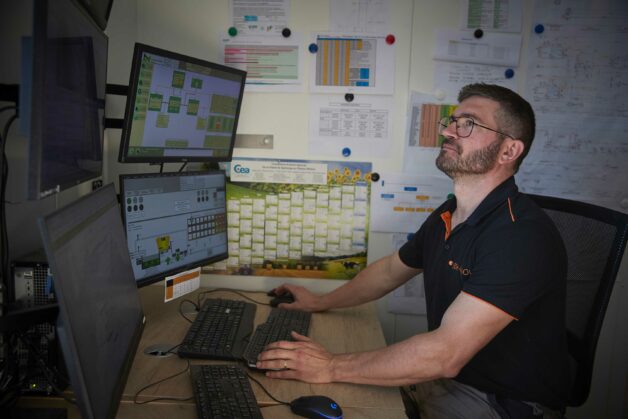
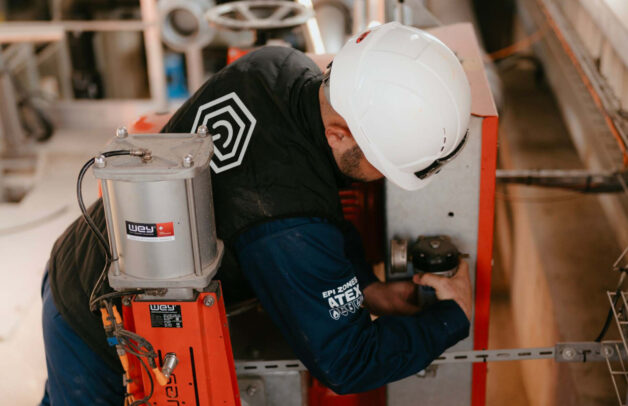
Commissioning
We carry out cold testing over a one- to two-week period to check the equipment and sensors. We then move on to hot testing: mixing the liquids and solids, seeding with sludge, feeding the digester until maximum flow rate or power is reached, after which we monitor performance for 21 days.
Naskeo audits and guarantees
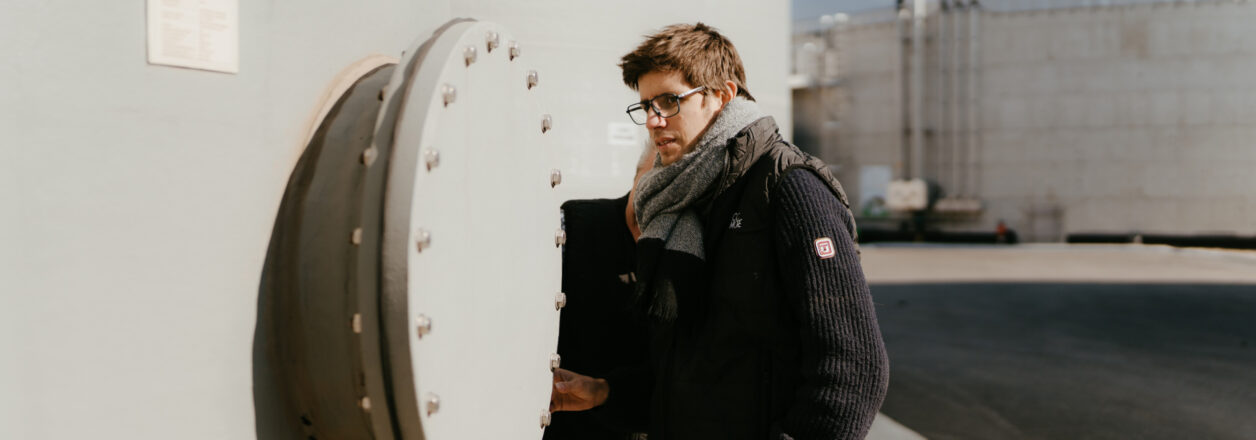
To ensure the quality of the biomethane plant and that it performs as planned, it is important to carry out a number of tests during the main phases of the build. We therefore conduct the following tests during construction, up until commissioning:
• Foundation testing
• Ensuring the tanks are watertight
• Network water/air tests
• Biogas quality control
• Feedstock testing (analyses)
• Biological monitoring of digester(s)
• Long-term performance tests
Our mixing systems
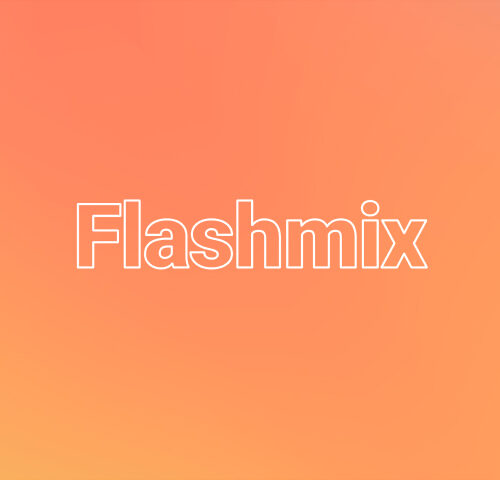
Direct mixing solution, suitable for easy-mix feedstock, robust and low-energy choice.
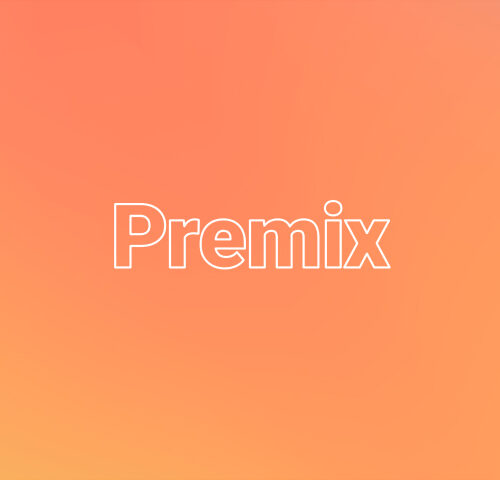
Low-profile mixing system, suitable for fibrous feedstock, grinds fibres to optimise the delivery rate of the feedstock’s methane potential. This system also features DRS® technology, which removes unwanted elements (pebbles, pieces of metal), helping avoid any machine failures or halts in production.
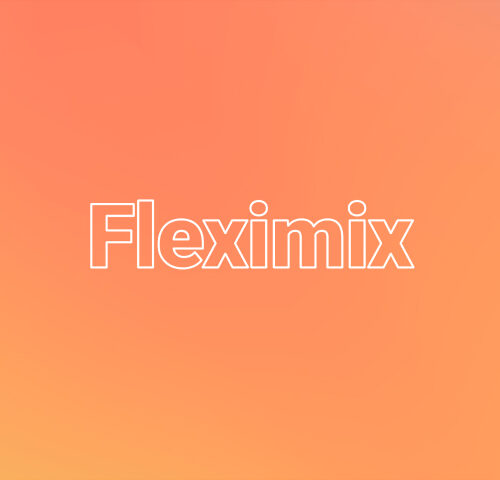
A mixing system suitable for complex feedstocks containing high levels of manure or fibrous material. It agitates and mixes the feedstock to prepare and homogenise it. It also removes up to 95% of unwanted elements from the feedstock (sand, gravel, pebbles, wood, metal).
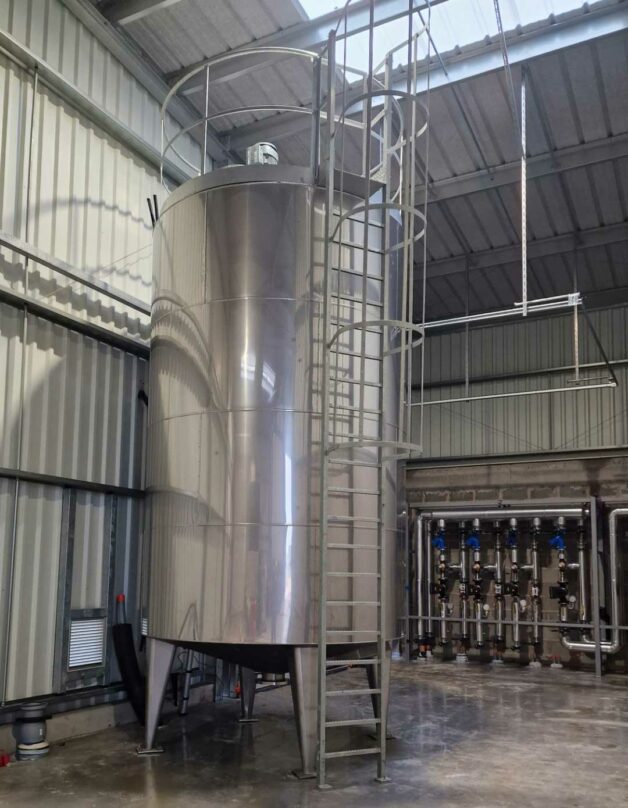
Our hygienisation
systems
A hygienisation solution for animal by-products with a built-in heat recovery system. This system is suitable for plants that process between 3,000 and 30,000 tonnes of waste per year. It is equipped with several devices to filter out unwanted material (glass, plastic, etc.) and produces high-quality slurry.
Hydrolysis
When rapid-kinetic feedstock exceeds 30% of total feedstock tonnage, we advise adding in a hydrolysis stage to separate it from the acidogenesis (rapid phases) and the following steps (slow phases). This guarantees biogas production, feeds the digester with a controlled mix of feedstock with stable levels of volatile fatty acids, and traps any unwanted material in the feedstock.
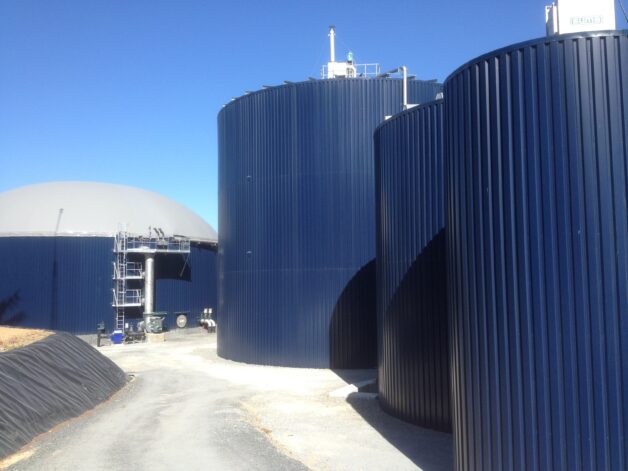
Digestion
Digestate treatment
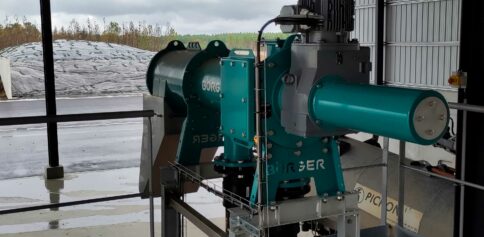
Screw press
After digestion, the digestate can be immediately stored or separated using a screw press. This provides you with liquid and solid digestate, which have differing agronomic properties and are suited to different crops.
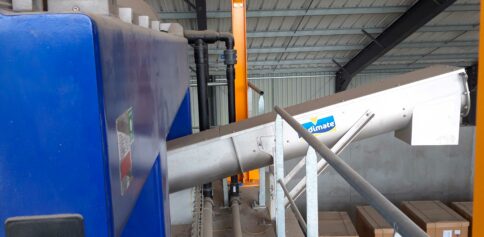
Centrifuge
Based on the type of feedstock (and thus the digestate as well), we can install a highly effective centrifugal separation system.
Storing the digestate
We offer several different storage solution, each sized to ensure sufficient autonomy and to allow you to spread your digestate in a way that is best suited to the crops being grown:
Biogas recovery
We can offer several different methods of biogas recovery.
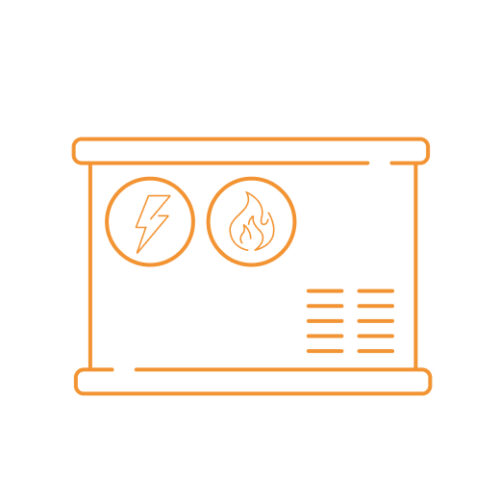
Cogeneration
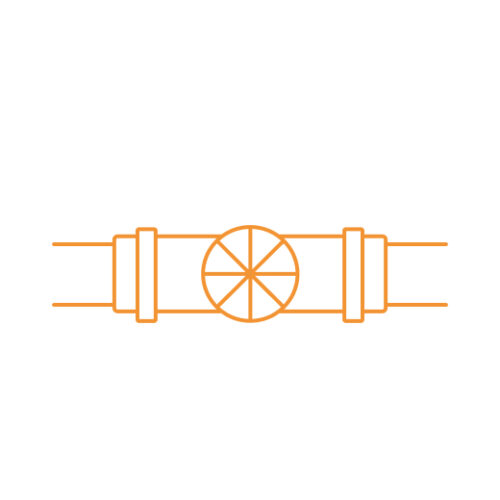
Biomethane injection
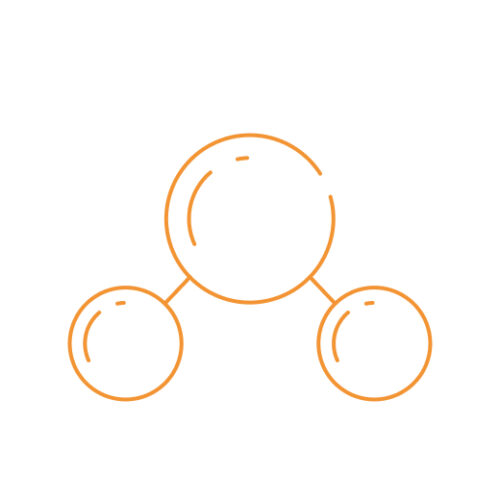
CO2 recovery
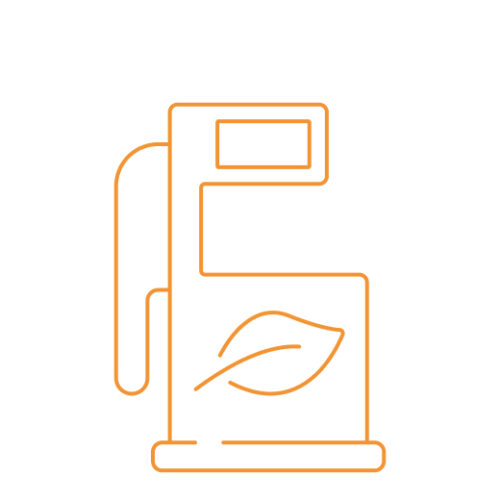
BioNGV transport